Welding Trends to Watch for in 2023 and Beyond
Welding is an integral part of many manufacturing and construction processes, and as technology advances, the field is undergoing significant changes. Whether you're a welder, welding contractor, or part of a manufacturing or construction company, staying up to date on the latest developments in the field is essential. So let's take a closer look at the trends that are shaping the future of welding.
Materials
One of the most significant trends in welding is using new and advanced materials. In recent years, manufacturers have been developing new alloys, composites, and other more durable and lightweight materials than traditional metals. These materials require new welding techniques and approaches to ensure optimal results, and as a result, welders must be trained on these new materials and processes.
Aluminum-Lithium Alloys
Aluminum-lithium alloys are becoming increasingly popular in the aerospace industry because they are lighter and stronger than traditional aluminum alloys. This has led to professionals developing new welding techniques specifically designed for welding aluminum-lithium alloys, such as friction stir welding. Composite materials, such as carbon fiber and fiberglass, are becoming more common in the automotive and wind energy industries. These materials require special welding processes and techniques to ensure a strong and secure bond.
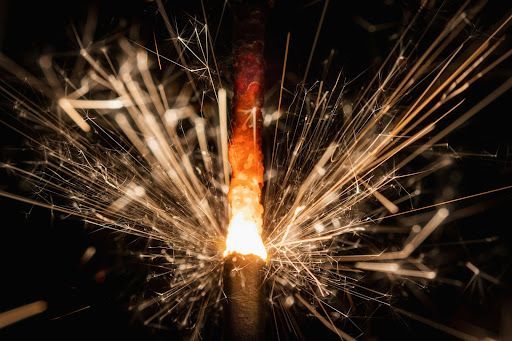
Techniques
In addition to new materials, advances in welding techniques are also driving changes in the industry. For example, automated welding techniques, such as robotic and laser welding, are becoming more popular due to their efficiency, accuracy, and ability to reduce human error. These techniques allow manufacturers to produce high-quality products quickly, which can help reduce costs and improve productivity.
Robotic Welding
Robotic welding is a promising trend, as it allows for consistent, high-quality welds, even on complex and irregular shapes. This is especially beneficial for automotive, aerospace, and energy companies, where precision is of the utmost importance. Further, robots can work 24/7 and do not require breaks, which can help to increase productivity and reduce labor costs.
Laser Welding
Laser welding is another advanced welding technique that is becoming more popular. This process uses a high-energy laser beam to melt the metal and create a strong bond. The laser beam is precisely controlled, which allows for very accurate welds, even on small and intricate components. This process is beneficial for welding delicate and complex parts, such as those used in medical devices and electronics.
Safety Features
Safety is always a top priority in welding, and recent developments in the industry have led to several new safety features. For example, many welding helmets now include auto-darkening lenses, which automatically adjust the tint of the lens to protect the welder's eyes from the bright light produced during the welding process. Many welding machines now include safety features such as emergency stop buttons and over-current protection, which help to prevent accidents and protect workers.
Personal Protective Equipment
Another significant trend in welding safety is the use of personal protective equipment (PPE). This includes welding gloves, protective clothing, and eye protection, which help to protect welders from the heat, sparks, and fumes generated during the welding process. Many welding companies are now investing in air-purifying respirators and other breathing protection devices, which help to protect workers from harmful fumes and vapors generated during the welding process.
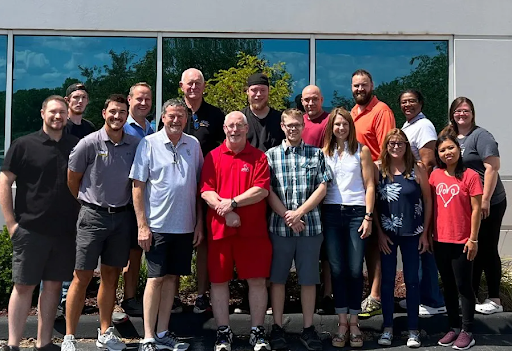
KDAR Company Is Here To Help
Our team at KDAR Company is ready to be your go-to wholesaler. We specialize in welding equipment (check out our Hot Max Torches) and cable ties – and we have many other products available as well.
Contact us today to get started!