How to Build a Welding Career
Welding is a highly skilled trade that is vital to the U.S. economy. It is an essential process for constructing buildings, bridges, ships, and many other types of infrastructure. Welding is also crucial in the manufacturing industry, where it is used to create a wide range of products, from cars and airplanes to appliances and electronics.
As a result, there is a high demand for skilled welders in the United States, making it a great career option for those interested in working with their hands and building things. This blog post will discuss how to build a career as a welder, starting with the skills and talents that make a good welder.
Importance of Welding
The world of welding goes deep, and there are many opportunities for anyone interested in building a career. Like some other trades, welding is accessible because it doesn't necessarily require a traditional 4-year college degree. A typical American welder earns an
average of $54,000 a year, although this is variable depending on the type of welding, geographic area, and skill level. Welders learn skills as they go, but the most important requirement for someone interested in building a career as a welder is attention to detail and not being afraid of some heat.
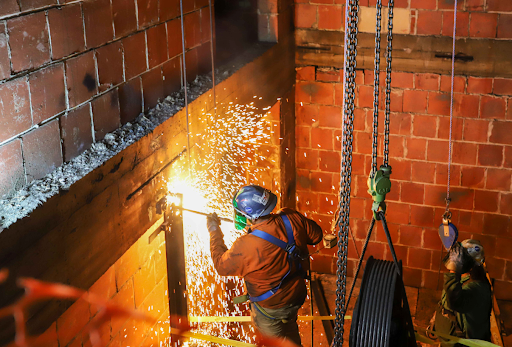
Skills and Talents for Welders
Welding requires a unique set of skills and talents, including:
- Attention to Detail: Welding involves precise measurements and intricate work, so attention to detail is crucial.
- Manual Dexterity: Welders must have excellent hand-eye coordination and manual dexterity to work with the tools and equipment involved in welding.
- Physical Stamina: Welding can be physically demanding, so it's essential to have the stamina to stand, crouch, or kneel for long periods.
- Technical Knowledge: Welders must have a strong understanding of welding techniques, materials, and safety procedures.
- Problem-Solving: Welders often encounter unexpected challenges and must be able to think on their feet to find solutions.
Where to Start After High School
If you're interested in becoming a welder, there are several paths you can take after high school. One option is to enroll in a welding program at a trade school or community college. These programs typically last between six months and two years and provide hands-on training in welding techniques, materials, and safety procedures. Another option is to find an apprenticeship program offering on-the-job welding training. These programs can take two to four years to complete and provide real-world experience working with experienced welders.
Different Types of Welding
There are several different types of welding, each with its unique set of techniques and materials. Some of the most common types of welding include:
- MIG Welding: A popular type of welding that uses a wire electrode to heat and join two metal pieces together.
- TIG Welding: A more precise type of welding that uses a tungsten electrode to create a clean, strong weld.
- Stick Welding: An older technique that uses a consumable electrode to combine two metal pieces.
- Flux-Cored Welding: A type of welding that uses a flux-cored wire to create a robust and clean weld.
How to Progress Through Different Job Titles
As you gain experience and skills in welding, you can progress through different job titles and positions. Some common career paths for welders include:
- Welder: As a welder, you will create high-quality welds according to precise specifications.
- Welding Inspector: Welding inspectors ensure that welds meet quality standards and regulations.
- Welding Supervisor: Welding supervisors oversee welding projects and manage teams of welders.
- Welding Engineer: Welding engineers are responsible for designing welding processes and developing new welding techniques and technologies.
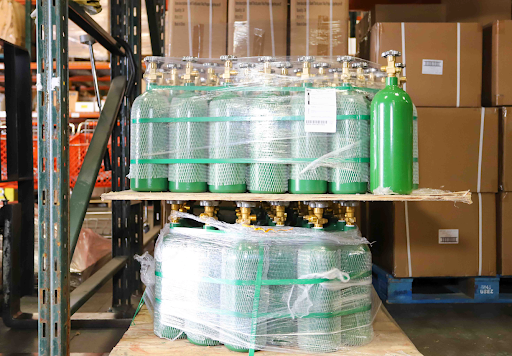
Welding in the Future
In recent years, there have been significant innovations and trends in welding that are worth watching. One of the most notable trends is the increased use of automation and robotics in welding, which can improve efficiency and reduce the risk of injury for welders. Another trend is the development of new welding techniques, such as friction stir welding, which allows for stronger, more reliable welds in certain materials.
Additionally, there is a growing focus on sustainability in welding, with companies seeking to reduce waste and energy usage in the welding process. As technology advances, we'll likely see even more innovations and trends in welding in the coming years, making it a great field to be involved in.
Work With KDAR
Our team at KDAR Company is ready to be your go-to wholesaler. We specialize in welding equipment (check out our Hot Max Torches) and cable ties – and we also have many other products available. Contact us today to get started!