Welding Safety In Hot Weather
When you run a business with employees welding or working in a warehouse, it’s critical to know how extreme weather affects them on the job. With summer around the corner, it’s time for a refresher on warehouse and welding safety in hot weather, so you know how to stock the gear and items that will help keep them safe.
Warehouses are inherently dangerous to work sites, to begin with, and that’s especially true if you’re a welder. Cooling off becomes difficult in an environment that doesn’t have safety measures in place. Heat-related illnesses like fatigue, loss of productivity, heatstroke, or even hospitalization can occur when body temperature becomes too high.
Warehouse managers must ensure that current summer warehouse safety procedures include these tips and best practices — on top of the measures already being taken.
Stay hydrated: Frequent water breaks should be encouraged, and plenty of potable water should be available for employees. Warehouse employees should be allowed to keep water bottles on their equipment when they’re working. This is probably the easiest way to make a considerable difference.
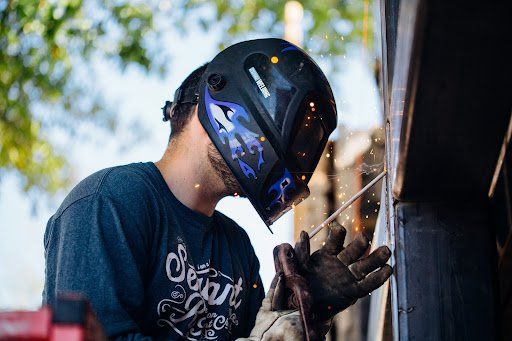
Keep up with maintenance: Warehouse managers should already have a regular maintenance schedule for your equipment, but it should be followed line by line during the summer. The warehouse manager should also create a list of additional maintenance tasks related to the effects of weather and heat.
Add ventilation: There’s a good chance there are already large, industrial-powered fans in most warehouses, but there’s also a good chance that they’re not doing enough to keep employees cool during the hot summer months. An experienced warehouse parts distributor can help warehouse managers learn about the best options and how to choose fans that work to help improve the overall energy efficiency of the warehouse.
Know the signs: Heat-related illnesses start gradually, with many signs of trouble ahead. Watch for these physical changes as precursors:
- Headaches
- Nausea
- Confusion
- Dizziness
- Heavy sweating
- Cramping
- Loss of consciousness
- Seizures
Upgrade equipment: If it’s been a while since the warehouse and its employees introduced new welding equipment, it might be time to research some upgrades. The same is true for virtually any other equipment (welding or not) used daily in the warehouse; extreme temperatures increase the rate of wear and tear and the risk for accidents.
Upgrade gear: The same can be said for the personal protective equipment that welders and other skilled warehouse workers use. Everything worn as PPE should fit well, not make welders uncomfortably hot or sweaty, and allow for full mobility during work. If the gear is old or worn down, it’s time to upgrade.
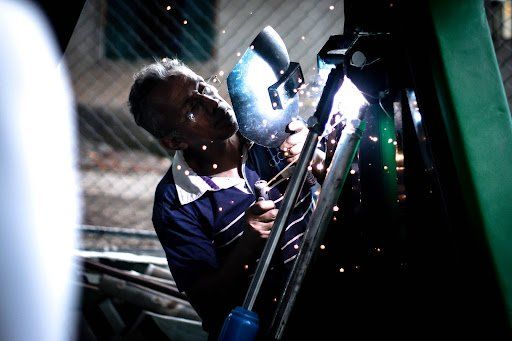
Invest In Quality
Making your customers’ warehouses safe this summer starts with offering top-quality gear and equipment. At KDAR Company, we understand that you want the best welding products for your customers at competitive prices. Count on our family-owned company to exceed your expectations in quality and service.
Take a closer look at the high-value welding safety equipment you’ll find at KDAR Company:
- Safety helmets, including a variety of welding helmets
- Premium auto-darkening welding helmets
- Colorful auto-darkening welding helmets
- Replacement ratcheting headgear
- Helmet lenses
- Goggles
- Helmet magnifying lenses
- Welding gloves
- Bulk safety glasses
- Grinding shields
- Hearing protection
- Dust protection
Since 1999, our family-owned wholesale company has supplied independent retailers across the United States, the Caribbean, Canada, and South America with superior welding safety equipment. The KDAR Company team brings over 40 years of retail experience to your store. We know the products customers want and help you get them for a lower price than our competitors offer.
Contact us today to learn more!