Innovation In Welding
Welding has been around for centuries. We can trace back welding to the Bronze Age, with examples of iron and gold being welded together during the era of the Ancient Egyptians. During the Middle Ages, blacksmithing was developed, but back then, items were produced by welding with a hammer.
These days, welding technology and techniques are being innovated and, in turn, helping other industries expand. Here are just a handful of ways that cutting-edge welding is helping projects in other worlds beyond manufacturing.
Friction Stir Welding
This process uses friction to join two workforces without melting the material – think clay or dough. It’s commonly used for welding two dissimilar materials and modern polymers and other structures that need high weld space. This method creates a low environmental impact and is increasingly being used in manufacturing lightweight, durable automotive and aerospace components.
Nanoscale Sculpturing
Imagine welding without the welding; that’s nanoscale sculpturing. It’s an alternative method of joining for connecting metals with metals and other polymers. It works at room temperature and doesn’t damage already coated or treated surfaces. This method is being used for applications like the interiors of ships and cars.
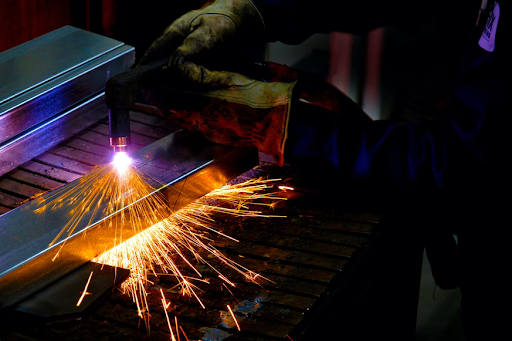
Natural Fiber Welding
Fiber welding joins the polymers within natural fibers for high-performance yarn and fabric without glue or resins. This could make the production of materials like denim much more sustainable, as fiber welding uses a significantly less volume of water and chemicals than the traditional fabrication and dying methods.
Plasma Welding
Although this method (similar to TIG welding) was introduced in the 1960s, it’s become much more mainstream in applications where application volume, consistency, and minimum downtime are considerations. This innovative method uses less energy, less space, and less noise, all three of which are challenges in welding.
Robotic Welding
Welding using machines or robots is one of the most common applications in industrial work, mainly in the automotive sector. It’s ideal for manufacturers who create products using high-volume, repetitive welding, like assembly lines. Quality assurance can be finetuned with tech components that collect data and create more accurate algorithms for workflows. Arc, laser, and plasma welding can all be used in robotic welding.
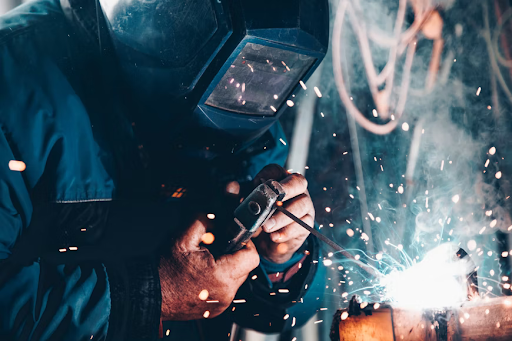
The Future Of Welding
We can’t wait to see what the future holds for innovation and growth within the field, and we ensure that our team stays ahead of welding trends to best educate our customers. Regardless of the tools and supplies you need to complete your welding project, we can help!
KDAR Company is a wholesale distributor of products to the welding, automotive, lawn and garden, and tool industries. Our products are sold under the US Trademark “Hot Max” brand. We focus on retail supply chains with innovative, high-quality products, and state-of-the-art packaging to sell at great prices.
Our goal is to sell high-quality make products with more features at competitive prices, all backed by excellent customer service. You will find us friendly, easy to work with, and enthusiastic about supporting your business.
Contact us to learn more!