Tips for Safe Welding During the Summer
Welding is an essential skill in many industries, from construction to manufacturing. However, welding in hot weather poses unique challenges that can impact safety and productivity. High temperatures, increased risk of dehydration, and heat-related illnesses are significant concerns for welders working in hot climates or during summer.
This blog post will provide comprehensive tips on staying safe and maintaining productivity while welding in hot weather.
Understanding the Risks
Welding in hot weather can lead to several health and safety risks, including:
- Heat Stress and Heat Stroke: Prolonged exposure to high temperatures can cause heat stress, which, if left untreated, can escalate to heat stroke. Symptoms include dizziness, nausea, confusion, and loss of consciousness, which can be fatal.
- Dehydration: Sweating in hot weather can lead to dehydration, reducing concentration and physical performance.
- Burns and Skin Damage: The combination of hot weather and the high temperatures involved in welding increases the risk of burns.
- Fatigue: Working in heat can quickly lead to physical exhaustion, impacting the quality of work and increasing the risk of mistakes and accidents.
Preparing for Hot Weather Welding
Preparation is vital to ensuring safety while welding in hot weather. Here are some steps to take before starting work:
- Hydrate: Drink plenty of water before, during, and after your welding shift. Avoid caffeinated and alcoholic beverages, as they can contribute to dehydration.
- Dress Appropriately: Wear lightweight, breathable, flame-resistant clothing. Avoid dark colors, as they absorb heat rather than reflect it. Use welding jackets made from materials designed for hot weather.
- Use Sun Protection: If you're working outdoors, apply sunscreen to exposed skin and wear a wide-brimmed hat when not wearing a welding helmet.
- Inspect Equipment: Ensure all welding equipment is in good condition and cooling systems, if applicable, function properly.
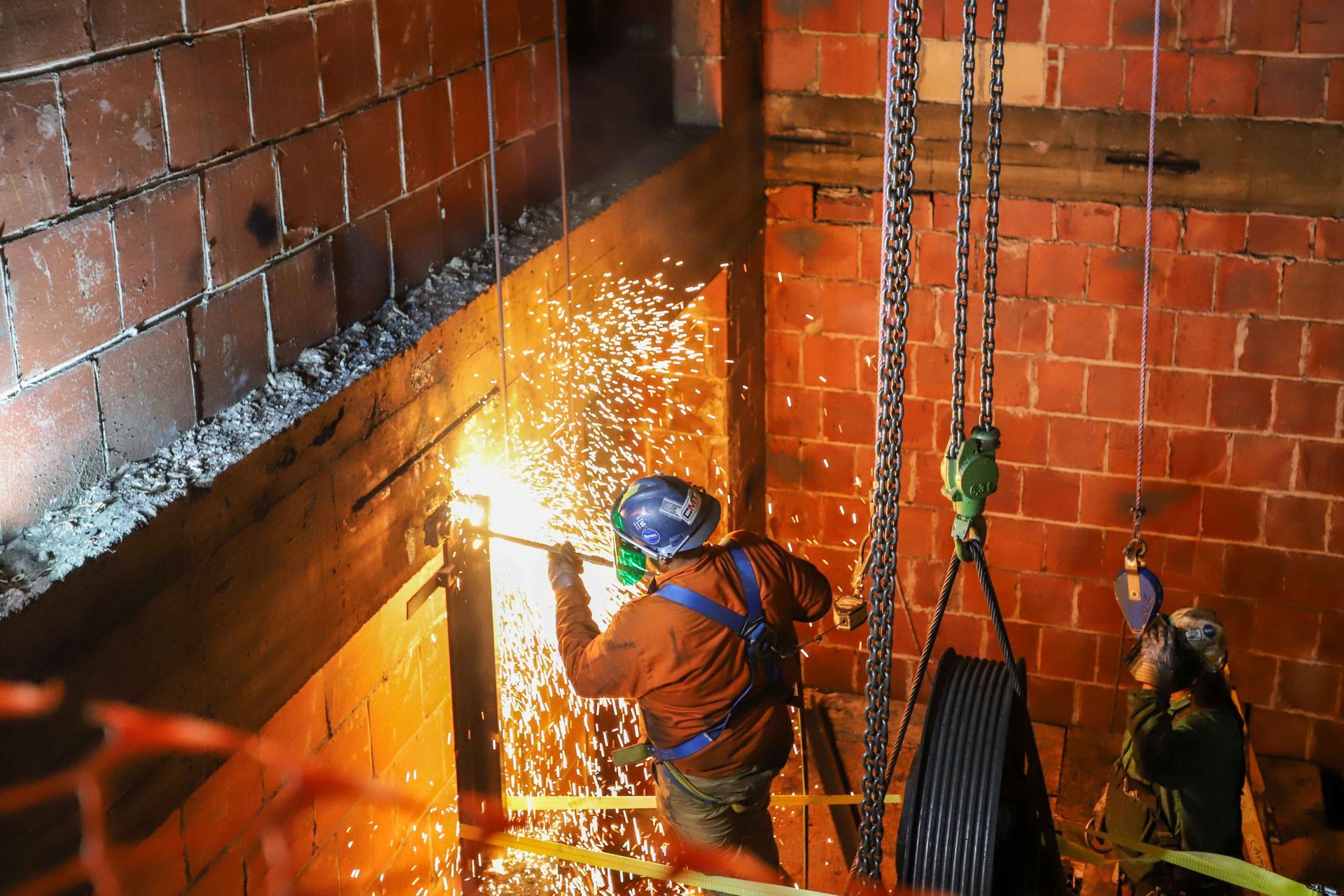
Tips for Staying Safe While Welding in the Heat
- Take Regular Breaks: Schedule frequent breaks in shaded or air-conditioned areas to cool down and rehydrate. Short, regular breaks are more effective than fewer, longer breaks.
- Monitor Health: Keep an eye on yourself and your coworkers' health. Watch for signs of heat stress, such as excessive sweating, rapid pulse, dizziness, or confusion.
- Use Fans and Ventilation: Use fans or portable air conditioners to improve airflow in the workspace. Proper ventilation helps reduce heat buildup and fumes.
- Adjust Work Hours: Schedule welding tasks during cooler parts of the day, such as early morning or early evening. Avoid working during peak heat hours.
- Pace Yourself: Work at a steady, manageable pace. Overexertion in hot weather can quickly lead to heat-related illnesses.
- Buddy System: Work with a partner who can watch for signs of heat stress and provide assistance if needed. A buddy system can be crucial in emergencies.
Maintaining Productivity
While safety is the priority, maintaining productivity in hot weather is also essential. Luckily, there are plenty of strategies to make this happen:
- Plan Ahead: Organize tasks to minimize exposure to heat (for example, complete intensive welding tasks during cooler parts of the day).
- Optimize Workflow: Use welding techniques and tools that reduce physical strain and time spent on tasks. If available, consider using automated welding machines.
- Stay Organized: Keep your workspace organized to reduce time spent searching for tools or materials. An efficient setup can help you work faster and more comfortably.
- Hydration Stations: Set up hydration stations with easily accessible water and electrolyte drinks. Staying hydrated helps maintain energy levels and concentration.
- Regular Maintenance: Ensure all equipment is well-maintained to prevent breakdowns that can lead to prolonged exposure to heat while troubleshooting.
Long-term Considerations
Investing in solutions that address heat-related challenges can improve both safety and productivity over the long term:
- Shade Structures: Erect temporary or permanent shade structures to protect outdoor work areas from direct sunlight.
- Cooling Equipment: Consider investing in portable cooling units or fans for your workspace.
- Training: Regularly train employees on heat-related safety practices and the importance of hydration and self-care in hot weather.
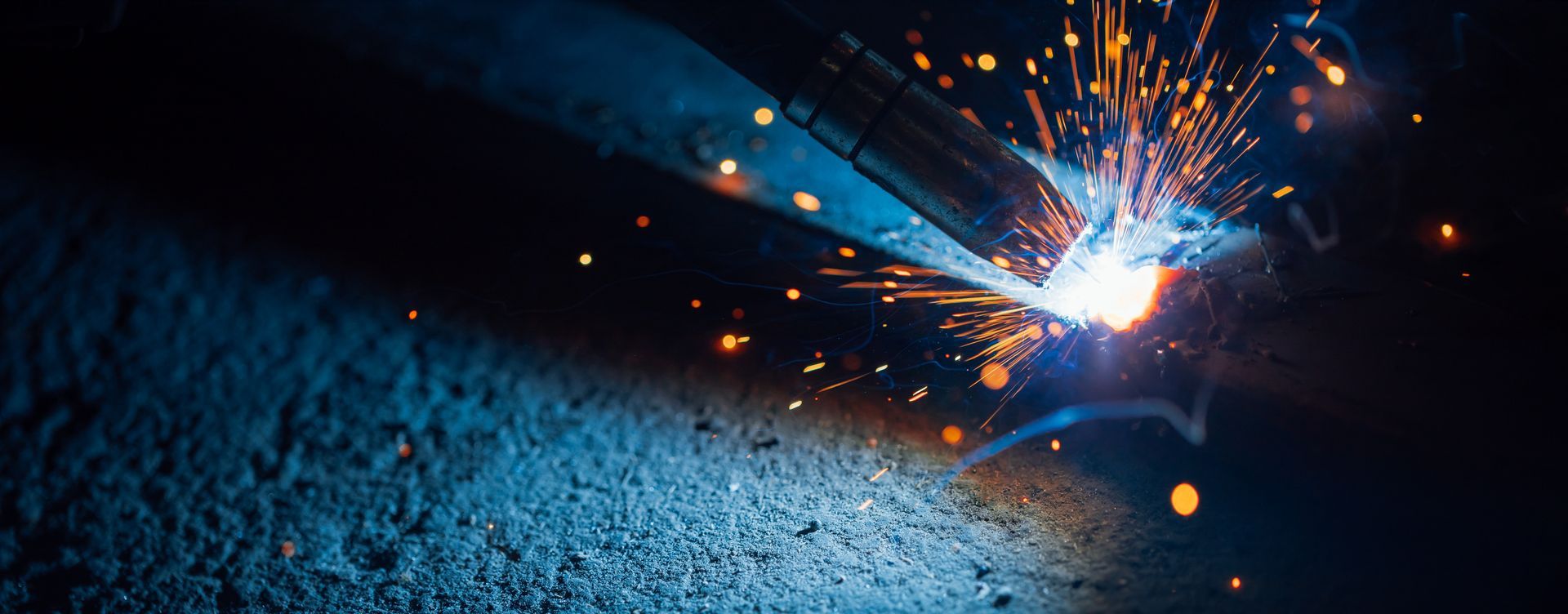
Work with KDAR Company
Welding in hot weather requires careful planning and adherence to safety protocols to prevent heat-related illnesses and maintain productivity. Prioritizing safety protects workers and ensures efficient, high-quality project completion.
At KDAR Company, we strive to provide welders with the equipment and support they need to do their jobs safely and efficiently, regardless of industry. Contact our support team to learn more!