The Future of Welding: Trends and Innovations Shaping the Industry
The welding industry is undergoing a significant transformation driven by technological advancements and changing market demands. As we look to the future, several trends and innovations are poised to redefine how welding happens, enhancing efficiency, safety, and precision.
In this blog post, we'll explore the future of welding and its implications for professionals and businesses alike.
Automation and Robotics
One of the most significant trends in the welding industry is the increasing adoption of automation and robotics. Automated welding systems and robotic welders are becoming more prevalent, offering several advantages over traditional manual welding. These systems provide consistent weld quality, increased productivity, and the ability to operate in hazardous environments without putting human workers at risk.
Robotic welding systems are particularly beneficial for repetitive tasks and high-volume production runs, where precision and speed are crucial. As technology advances, we can expect more sophisticated robotic systems capable of handling complex welding tasks, reducing the need for manual intervention.
Advanced Welding Processes
Innovation in welding processes is another area shaping the industry's future. Techniques such as laser welding, friction stir welding, and ultrasonic welding are gaining traction, each offering unique benefits for specific applications.
- Laser Welding: This process uses a focused laser beam to melt and join materials, providing high precision and minimal heat distortion. It's ideal for industries requiring fine detail work, such as electronics and aerospace.
- Friction Stir Welding (FSW): FSW is a solid-state joining process that uses frictional heat to soften and blend materials. It's particularly effective for welding aluminum and other lightweight alloys, making it a preferred choice in automotive and aerospace manufacturing.
- Ultrasonic Welding: This process utilizes high-frequency ultrasonic vibrations to create a solid-state weld by generating localized heat through friction. It's commonly used to join plastics and thin metals in the electronics and medical device industries.
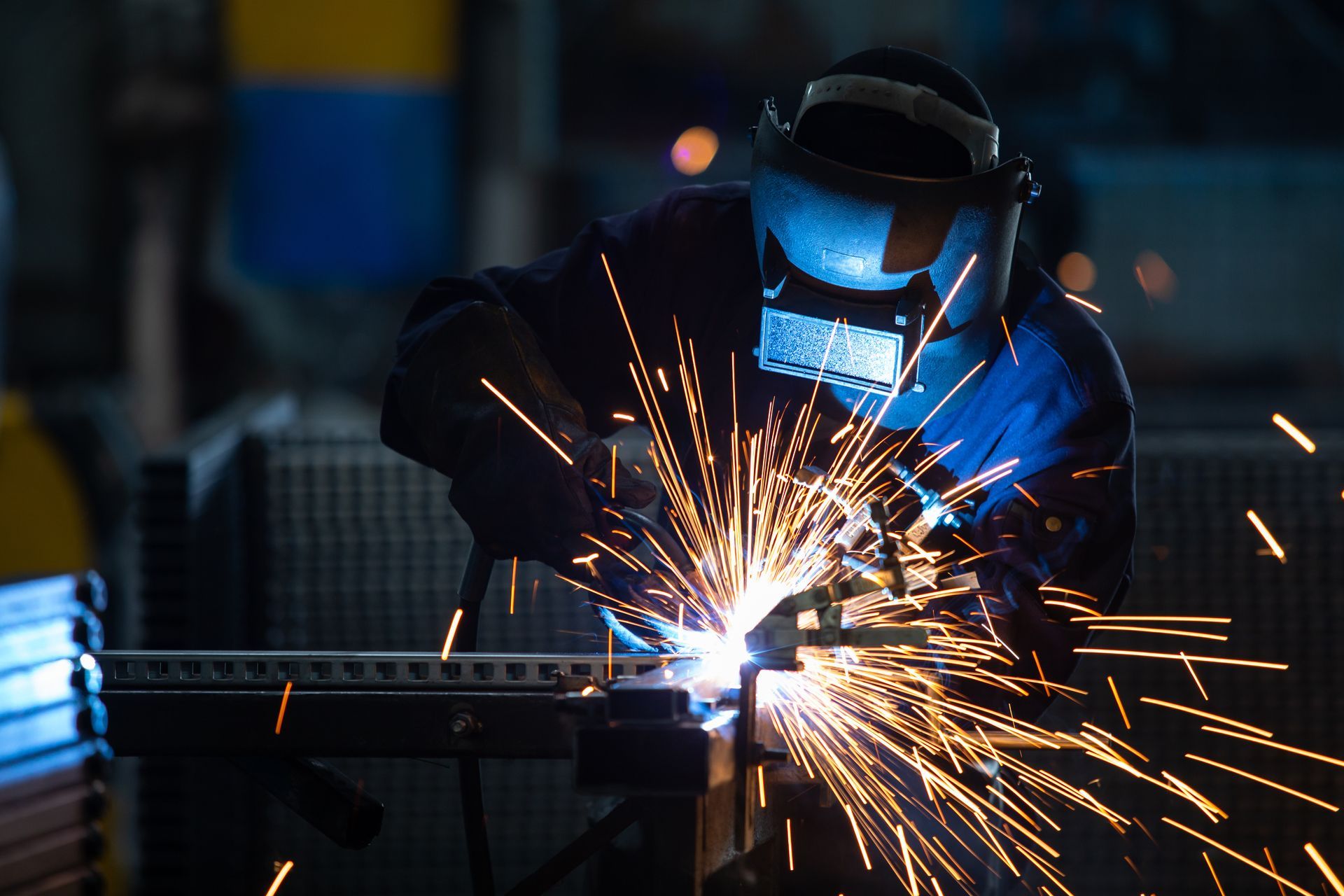
Digitalization and Smart Welding Technologies
Integrating digital technologies and the Internet of Things (IoT) is revolutionizing welding operations. Smart welding systems with sensors and real-time monitoring capabilities can collect and analyze data to optimize welding parameters, improve quality control, and predict maintenance needs.
These systems can provide welders with instant feedback, helping to identify defects and make adjustments on the fly. Additionally, augmented reality (AR) and virtual reality (VR) training programs are emerging as practical tools for skill development, allowing welders to practice in a simulated environment before tackling real-world projects.
Sustainable and Eco-Friendly Welding Practices
The welding sector is adopting greener practices as industries worldwide move towards sustainability. Innovations such as energy-efficient welding equipment, recyclable materials, and processes that reduce emissions and waste are becoming more prevalent.
For instance, cold metal transfer (CMT) welding is a low-heat process that minimizes spatter and reduces energy consumption, making it an eco-friendly alternative to traditional methods. Additionally, the development of bio-based fluxes and environmentally friendly shielding gases is helping reduce welding operations' ecological footprint.
Enhanced Safety Measures
Safety is a paramount concern in welding, and future advancements will enhance worker protection further. New protective gear with advanced materials and designs, such as lightweight welding helmets with enhanced visibility and respiratory protection, are being developed to improve comfort and safety.
Moreover, automated and robotic systems can perform hazardous tasks, reducing the risk of injury to human workers. Real-time monitoring and data analytics also play a crucial role in identifying potential safety hazards and implementing preventive measures.
Workforce Development and Training
The future of welding is not just about technology; it's about people. As the industry evolves, there is a growing need for skilled welders proficient in advanced techniques and technologies. Workforce development and training programs are essential to bridge the skills gap and prepare the next generation of welders.
Educational institutions and industry organizations increasingly offer specialized training programs incorporating the latest technologies, ensuring welders have the skills to thrive in a modern manufacturing environment.
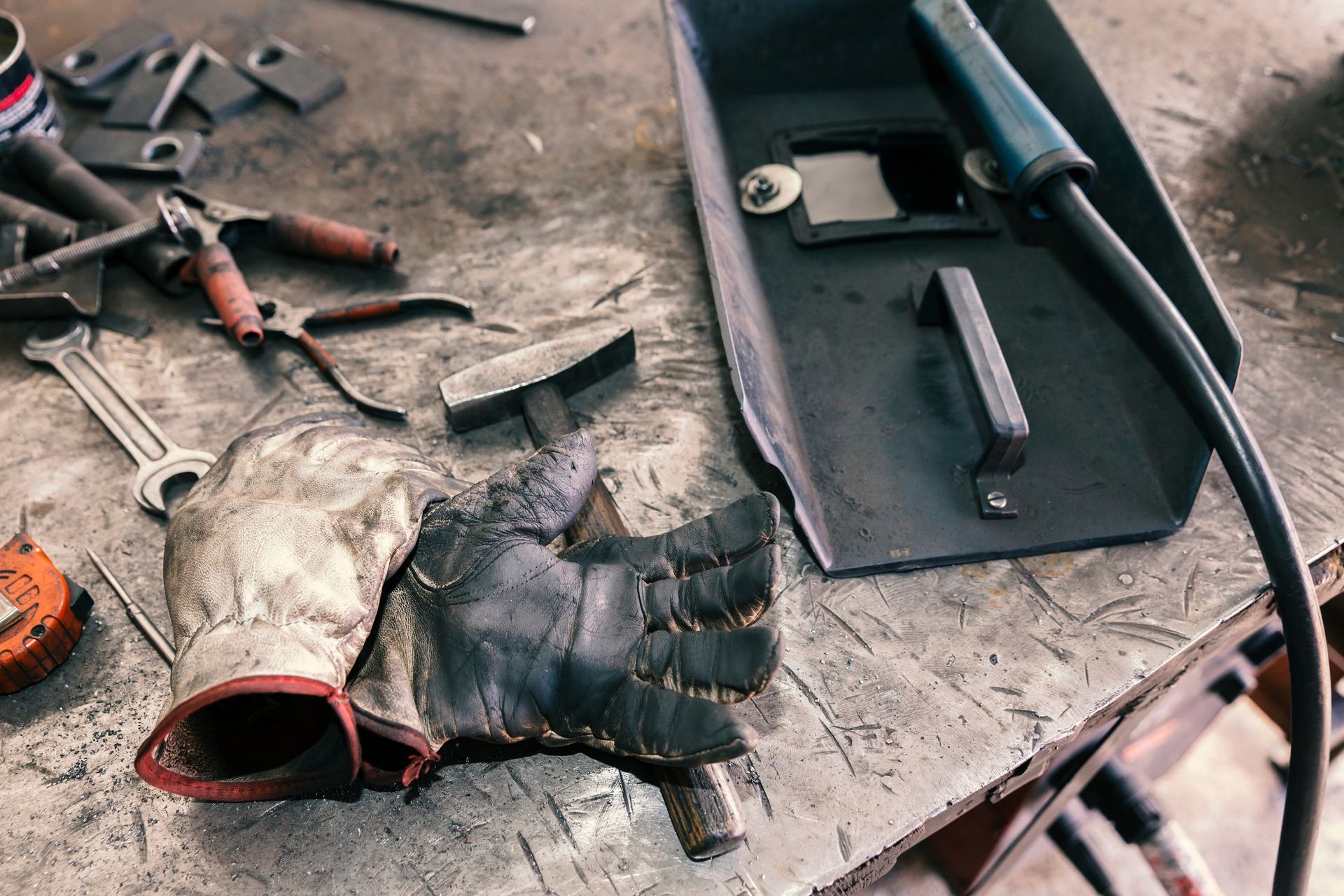
Work With KDAR Company
The future of welding is bright, with numerous innovations set to transform the industry. From automation and advanced welding processes to digitalization, sustainability, and enhanced safety measures, these trends will improve efficiency and quality and create new opportunities for skilled professionals.
As we embrace these changes, the welding industry will continue to play a vital role in driving technological progress and supporting economic growth. For businesses and welders alike, staying ahead of these trends will be critical to remaining competitive in a rapidly evolving landscape.
At KDAR Company, we strive to provide welders with the equipment and support they need to do their jobs safely and efficiently, regardless of industry. Contact our support team to learn more!