Tips for Safe Welding During the Fall
As the seasons change and fall rolls in, so do the challenges welders face in diverse environments.
Cooler temperatures, shorter days, and fluctuating weather conditions can all impact safety on the job.
Welding safety is always a priority, but fall introduces unique factors to protect welders, their workspaces, and those around them.
Here, we provide essential fall welding safety tips to ensure you stay safe and efficient as the season shifts.
Proper Ventilation in Enclosed Spaces
With fall temperatures dropping, it's tempting to close up doors and windows to keep the autumn chill out. However, proper ventilation is critical for welders to avoid inhaling harmful fumes.
Fumes generated by welding processes contain hazardous metals and gases, which can cause serious health issues when inhaled over time.
In the fall, there may be fewer opportunities for natural airflow in indoor welding spaces. To combat this:
- Ensure proper ventilation systems are in place and functioning correctly.
- Use fans or mechanical ventilation to keep fresh air circulating.
- If you're welding outdoors and the weather forces you into a temporary structure, such as a shed or tent, be mindful of how confined the space may be and ensure the use of fume extractors or other ventilation aids.
Addressing Fall Weather Conditions
Fall weather can be unpredictable, ranging from windy days to heavy rain (and even early snow in some regions). These environmental factors directly impact welding safety.
Wind can disperse shielding gas, rain can interfere with electrical equipment, and cold temperatures can change the properties of the materials you're working with.
When working outside, check the weather forecast and plan accordingly. Portable shelters or welding screens can protect from wind and rain while maintaining proper airflow.
In colder temperatures, preheat metal surfaces, as they tend to behave differently when cold, possibly resulting in brittleness or cracking. Preparing for these conditions will keep your work quality high while reducing safety risks.
Equipment and Material Maintenance
Fall is a great time to assess the condition of your welding equipment and materials before the harsher winter season sets in.
Temperature fluctuations, humidity, and moisture can all cause wear and tear on equipment like welding torches, cables, and hoses.
Inspect cables and hoses for cracks or leaks that may develop from weather exposure. Pay particular attention to consumables like electrodes and filler metals; they may not appropriately perform if exposed to moisture.
Always store materials in dry, temperature-controlled environments to prevent rust and other moisture-related issues. Routine equipment maintenance prevents costly repairs and enhances safety on the job.
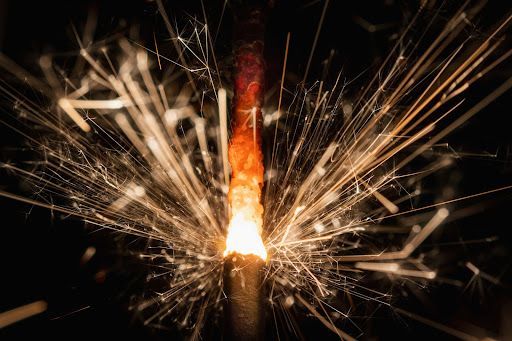
Fire Prevention and Hazard Awareness
Fall often means dry conditions, with leaves and other debris scattered around outdoor worksites. Working with welding tools that generate sparks and heat can become fire hazards.
Before you begin welding, clear the area of dry leaves, grass, or other flammable materials. If welding in a windy environment, be mindful of where sparks could travel, as they can ignite fires several feet away.
Always keep fire prevention equipment nearby, including fire extinguishers and fire blankets. Consider setting up welding screens that contain sparks, especially when working near combustible materials.
A proactive approach to fire safety is critical in preventing accidents during autumn.
Lighting and Visibility
As the days grow shorter, proper lighting becomes more important. Dim lighting can obscure your work, leading to precision errors and safety risks.
If you work outdoors, you'll have less natural daylight to rely on, which could mean reduced visibility in the early morning or late afternoon.
Ensure your work area is well-lit by using portable or stationary lights. LED work lights are beneficial because they provide bright, consistent illumination and are energy-efficient.
Battery or generator lights can help maintain visibility for outdoor sites, ensuring you can perform your job safely and accurately, even in lower-light conditions.
Personal Protective Equipment (PPE) Adjustments
With the colder weather, welders need to adjust their personal protective equipment (PPE) to ensure warmth and safety. Layering clothing may be necessary to stay warm.
Still, it's essential to ensure these extra layers don't interfere with mobility or pose additional hazards.
Use insulated welding gloves that protect against heat and warm your hands in cooler weather. Similarly, ensure your helmet, boots, and jackets are appropriately fitted to avoid discomfort or restricted movement.
Wet gloves or clothing can increase the risk of electrical shock, so always keep your PPE dry and replace it immediately if it becomes damp.
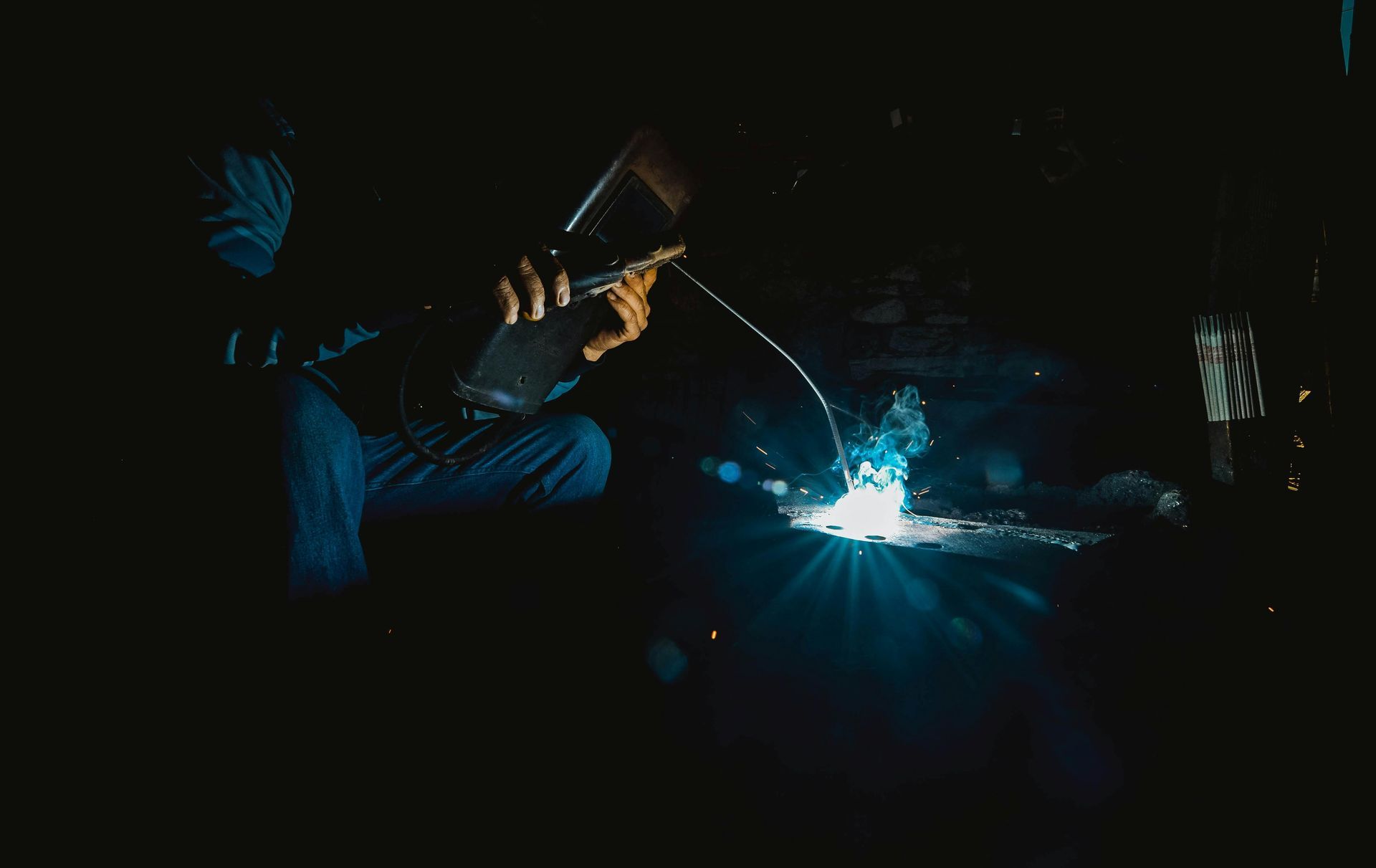
Staying Hydrated and Energized
One often overlooked aspect of welding in the fall is hydration. Cooler weather can mask signs of dehydration, leading to fatigue and slower reaction times, which can increase the likelihood of accidents.
It's important to keep hydrated throughout the day, even if you don't feel thirsty. Drink water regularly and take short breaks to rest and stay energized, especially during long welding sessions.
Work With KDAR Company
Welding safety is always a priority, but fall conditions require welders to take additional precautions. You can continue working efficiently and safely throughout the season by evaluating your safety practices now and making the necessary adjustments for the fall.
Whether you are a beginner or an experienced welder, returning to the basics ensures a solid foundation for continued learning and improvement in this vital trade.
At KDAR Company, we strive to provide welders with the equipment and support they need to do their jobs safely and efficiently, regardless of industry.
Contact our support team to learn more!