Essential Winter-Ready Pressure Washer Accessories
As winter approaches, it's time to prepare your pressure washer for the season.
Cold temperatures, snow, and ice bring unique challenges for cleaning and maintenance. Still, with the right accessories, you can keep your pressure washer in peak condition and even make it more effective.
This guide will cover essential pressure washer accessories designed to enhance performance, protect your machine, and make winter cleaning manageable and safe.
Protect Your Pump with Antifreeze Solution
Winter poses a significant risk to your pressure washer's pump. Water remaining in the pump or hoses can freeze and expand, causing cracks and leaks that can be costly to repair.
One of the easiest ways to avoid this is using an antifreeze solution designed specifically for pressure washers.
How It Works
To winterize your pressure washer, flush the antifreeze solution through the system after draining any remaining water; this keeps your pump and hoses safe from freeze damage and prepares your machine for a seamless start-up in the spring.
Plus, pressure washer antifreeze solutions are non-toxic and easy to store.
Quick-Connect Nozzles for Fast Winter Cleanups
In colder months, grime, salt, and snow residue can quickly build up on outdoor surfaces, making them more challenging to clean.
Quick-connect nozzles are an excellent accessory for this purpose. They allow you to easily switch between different spray patterns, resulting in more efficient cleaning of various surfaces.
A quick-change setup can make winter cleaning easier when dealing with ice and winter gunk.
Top Nozzle Choices for Winter:
- 15-degree Nozzle: Ideal for breaking up heavy grime and salt.
- 25-degree Nozzle: Perfect for general wood, concrete, or metal cleaning.
- Soap Nozzle: Use this to apply detergent on oily or heavily soiled surfaces, which is common in winter.
Switching between nozzles is easy and saves time, making it a perfect solution for finishing outdoor tasks quickly in the cold.
Heated Pressure Washer Hose for Reliable Water Flow
Cold weather can cause regular hoses to freeze, making them stiff and difficult to work with.
Heated pressure washer hoses prevent this by maintaining a warm internal temperature, allowing water to flow freely even in freezing conditions; this makes heated hoses a valuable upgrade for winter, whether washing a vehicle, clearing driveways, or tackling other cold-weather cleaning tasks.
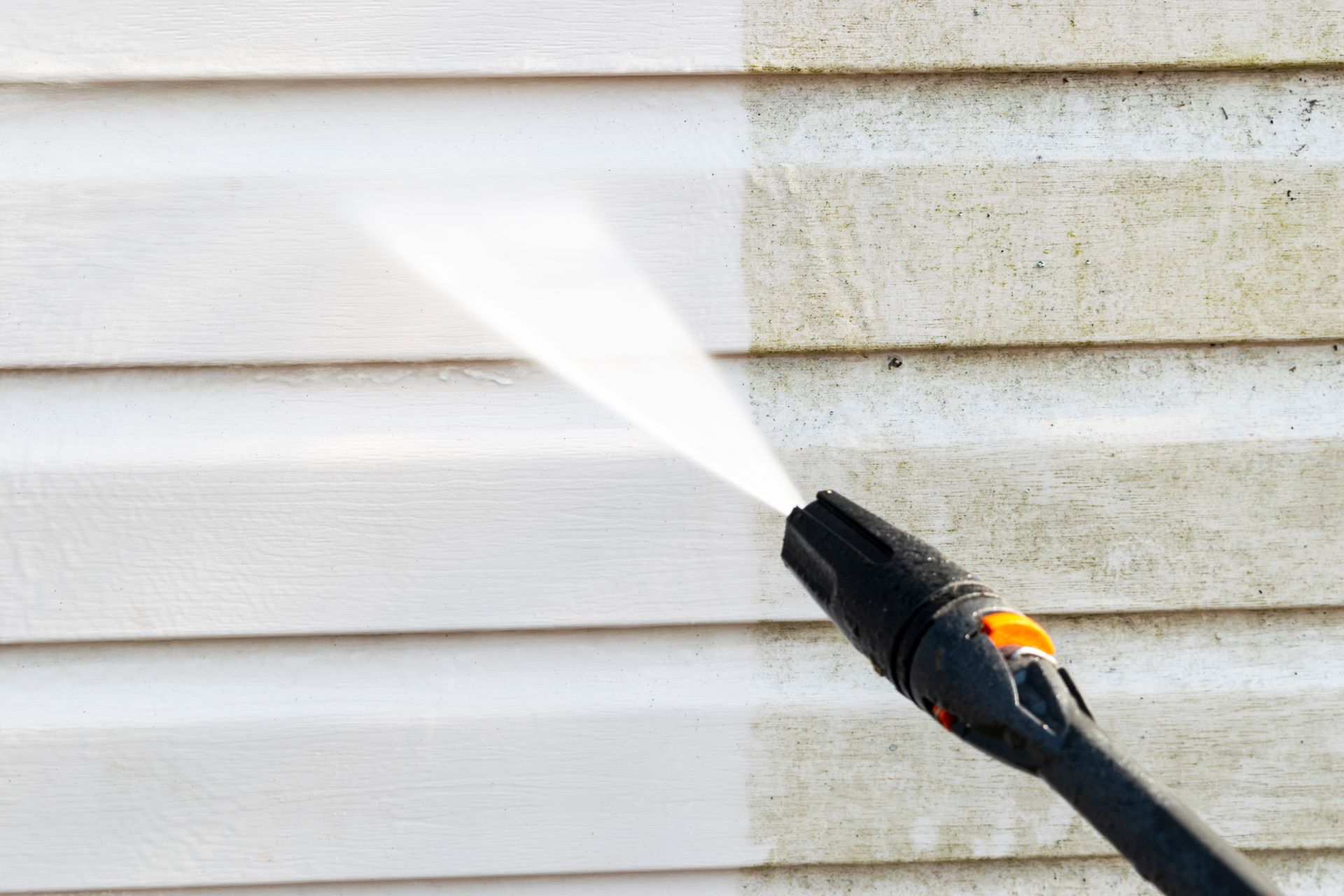
Surface Cleaners: Remove Winter Salt and Grime
A surface cleaner is one of the best tools for dealing with winter grime.
These accessories attach to your pressure washer and feature spinning nozzles that apply an even, circular clean on flat surfaces. For winter cleaning, surface cleaners are incredibly efficient at removing compacted dirt, road salt, and snow residue from driveways, sidewalks, and patios.
Using a surface cleaner means faster results with less effort, leaving outdoor surfaces free of slippery dirt and grime—a big plus when winter mess is a daily occurrence.
Cold-weather O-rings and Seals
Standard rubber seals and O-rings in your pressure washer can become brittle when temperatures drop, leading to cracks and leaks.
Cold-weather O-rings and seals are made from flexible materials in low temperatures, ensuring a better seal and reducing the chance of leaks.
Replacing your existing seals with these winter-ready options is an easy way to keep your pressure washer working smoothly, especially if you're cleaning in frigid weather.
Winter Detergents and De-Icer Solutions
Winter brings dirt and grime, road salt, oil, and other substances that can damage surfaces if left untreated. Using winter-specific detergents or de-icer solutions with your pressure washer makes cleaning more effective.
De-icers are especially helpful for breaking down ice buildup on walkways, while detergents help cut through greasy, oily residue from winter road conditions.
How to Apply Winter Detergents:
Attach a detergent nozzle to your pressure washer, apply the solution to the surface, let it sit for a few minutes, then rinse with clean water. This combination helps prevent re-icing and leaves surfaces cleaner.
Use Winter-Grade Pressure Washer Oil
Thickened oil can make starting your pressure washer engine difficult in cold weather.
Switching to winter-grade oil, which stays fluid at lower temperatures, reduces strain on the engine and makes start-up easier. Winter-grade oil is formulated to keep your pressure washer performing efficiently, and it's an essential accessory for those who frequently clean in cold weather.
Insulated Pressure Washer Cover for Storage Protection
When you're not using your pressure washer, it's essential to store it correctly to protect it from the cold.
An insulated cover is a simple but effective way to shield the machine from snow, ice, and extreme temperatures. These covers often feature water-resistant materials and insulation to keep internal components safe.
Some even come with pockets for storing accessories, so you can keep everything organized and ready for next season.
Consider Upgrading to a Hot Water Pressure Washer
Consider a hot water pressure washer if winter cleaning is a regular routine.
Unlike standard models, hot water pressure washers heat the water before it's ejected, making it easier to clean stubborn dirt, grease, and ice buildup.
Though more costly, these models can be a worthy investment for frequent winter cleaning, as they reduce the time and effort needed to tackle challenging tasks.
However, if upgrading isn't an option, using the right cold-water pressure washer accessories will still significantly improve winter cleaning efficiency.
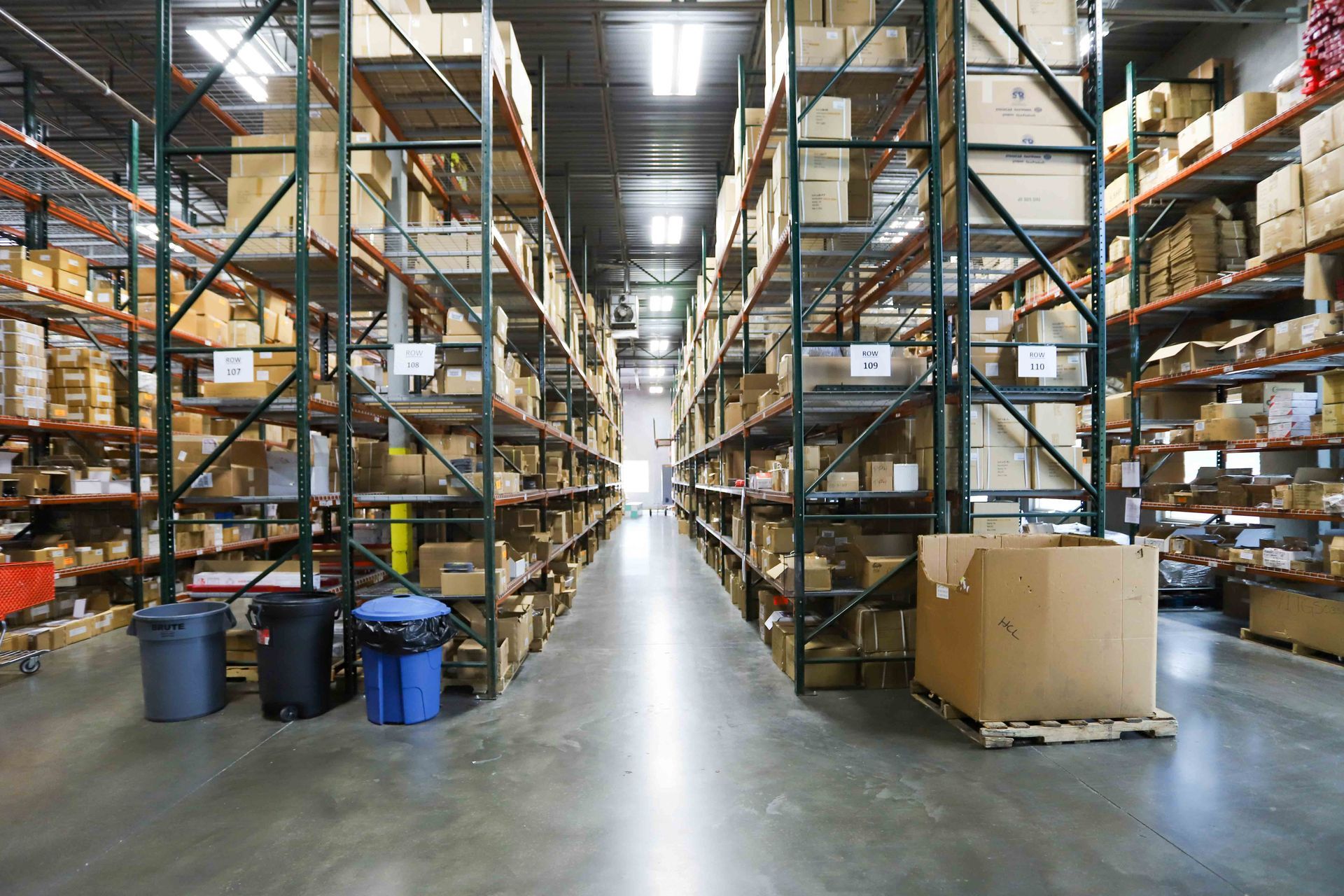
Get In Touch With KDAR Company
Preparing your pressure washer for winter use involves a few simple but crucial steps.
Investing in winter-specific accessories—like antifreeze solution, heated hoses, surface cleaners, and insulated covers—can protect your equipment from the elements and make cold-weather cleaning more manageable.
Whether clearing away road salt, tackling greasy grime, or simply storing your machine, these accessories will keep your pressure washer winter-ready and in top condition for years.
Still, we advise using caution and common sense when planning out your cold-weather pressure-washing projects. Evaluate your equipment, the weather conditions, and the parameters of the job before starting. A general rule of thumb is to avoid using a pressure washer when the temperature falls below 40 degrees Fahrenheit.
At KDAR Company, we strive to provide welders with the equipment (including a large variety of hose clamps)and support they need to do their jobs safely and efficiently, regardless of industry. Contact our support team to learn more!