A Comprehensive Guide to Hose Clamps
Hose clamps are versatile and essential components used in various applications, from welding projects to automotive repairs. When selecting the right clamp, it's crucial to consider factors like material compatibility, temperature resistance, and pressure ratings to ensure durability and performance.
Understanding factors like adjustability, ease of installation, and vibration resistance ensures the clamp's longevity and connection security. Beyond their traditional use, hose clamps offer innovative applications in areas like cable management, automotive repairs, and DIY projects, making them versatile tools for both industrial and creative needs.
Material Compatibility
Material compatibility is essential for ensuring durability and performance when selecting hose clamps for your welding project.
Stainless steel is often the material of choice due to its superior resistance to rust and corrosion, which is crucial in the high-temperature and potentially corrosive environment of welding.
Stainless steel hose clamps, such as those made from 304 or 316 stainless steel, offer excellent mechanical strength and resistance to oxidation.
For environments with extreme conditions, such as exposure to acidic substances or high salinity, 316 stainless steel clamps provide enhanced corrosion resistance compared to 304.
Always verify that the hose clamp material aligns with the welding process and the surrounding environmental factors to prevent premature failure and enhance longevity.
Temperature Resistance
Welding processes involve significant heat generation; ordinary hose clamps might not withstand these temperatures.
High-temperature silicone or
heat-resistant rubber clamps are best for handling thermal stress and preventing failure under high-heat conditions.
For instance, silicone clamps can typically handle temperatures ranging from -65°F to 600°F (-54°C to 315°C), making them suitable for high-temperature applications.
Additionally, some clamps are coated with materials that protect against heat and flames, ensuring they remain effective even under extreme conditions.
Always check the manufacturer's specifications for temperature resistance to ensure the clamps will perform reliably throughout your welding project.
Pressure Ratings
Understanding the pressure requirements of your welding system is critical for choosing the right hose clamps. Clamps are rated for different pressure ranges, and using a clamp with insufficient pressure capacity can lead to leaks or system failures.
Consider clamps with robust pressure ratings and reinforced designs for high-pressure applications, such as those involving gases or hydraulic systems.
Heavy-duty clamps or those with reinforced bands are best for high-pressure scenarios. Always consult the clamp manufacturer's pressure rating documentation to match the clamp's capacity with your system's requirements.
Corrosion Resistance
Exposure to moisture, chemicals, and other corrosive elements is common in welding environments. To ensure long-term reliability, hose clamps must be resistant to corrosion.
Stainless steel clamps, particularly those with a coating or passivation treatment, provide excellent resistance to rust and corrosion. In some cases, clamps with additional coatings, such as zinc plating or black oxide, offer extra protection against harsh environmental conditions.
For projects involving highly corrosive substances, consider clamps designed explicitly for chemical resistance, which can offer enhanced durability.
Size and Diameter
Choosing the correct size and diameter of hose clamps is crucial for creating a secure connection and preventing leaks. Clamps are available in various sizes to fit different hose diameters.
Adjustable hose clamps, such as worm drive clamps, provide flexibility in accommodating a range of hose sizes. To ensure a proper fit, measure the outer diameter of your hoses accurately and select clamps that match this measurement.
Using too small clamps can lead to inadequate clamping force and potential hose slippage, while clamps that are too large might not provide a tight seal.
Installation Method
Different types of hose clamps require various installation methods.
Screw-type clamps (worm drive) need a screwdriver or wrench for tightening, while
quick-release clamps offer tool-free installation and removal, enhancing convenience for frequent adjustments.
Consider the installation tools and techniques required for each clamp type, and choose ones that align with your workflow.
Another option is
automatic tensioning clamps, which self-adjust to maintain consistent pressure, reducing the need for manual tightening.
Adjustability
Over time, hoses may expand or contract due to temperature changes or wear.
Adjustable hose clamps allow you to modify the tightness or diameter to accommodate these changes. Worm drive clamps, for instance, feature a screw mechanism that can tighten or loosen to fit different hose sizes.
Clamps with constant tension designs maintain a consistent clamping force, beneficial in environments with fluctuating temperatures or vibrations.
Select clamps with sufficient adjustability to ensure a reliable and secure connection throughout the lifecycle of your welding project.
Vibration Resistance
Welding operations often involve vibrations that can loosen hose connections.
To address this issue, opt for hose clamps with
vibration-resistant features, such as locking mechanisms or constant tension designs.
Vibration-proof clamps, including those with internal springs or unique locking systems, can withstand continuous movement and prevent loosening; this ensures the hose connections remain secure and prevents potential leaks or damage during operation.
Accessibility
In welding setups, hose clamps might be in hard-to-reach areas. When selecting clamps, consider the ease of access.
Low-profile clamps or those designed for tight spaces can simplify installation and adjustments.
Some clamps feature
ergonomic handles or
quick-release mechanisms for easier access in confined areas.
Ensuring the easy reachability of clamps for maintenance or replacement can significantly reduce downtime and enhance the efficiency of your welding operations.
Specialized Applications
Specialized hose clamps may be necessary for welding projects with unique requirements. These include clamps for
extreme temperatures,
high-pressure environments, or
chemical resistance.
For instance, high-pressure clamps will withstand intense pressures, while chemical-resistant clamps are suitable for environments where the clamps face exposure to corrosive substances.
Research and select clamps designed for your application's unique challenges to ensure optimal performance and safety.
Innovative Uses of Hose Clamps
Hose clamps are incredibly versatile and can be used innovatively beyond traditional applications. Here are some examples:
- Cable Management: Use hose clamps to organize and secure electrical cables and wires, providing a neat and orderly appearance while preventing tangling and damage.
-
DIY Projects: Hose clamps can serve as mounts or supports for various items, such as garden hoses, hand tools, or even custom shelving systems, in home improvement and DIY projects.
-
Temporary Fixes: Employ hose clamps for temporary repairs on hoses, pipes, or other components. Their adjustability and strong clamping force make them ideal for emergency fixes.
-
Heat Shields: Use hose clamps to attach heat shields or insulation materials to prevent heat damage in areas exposed to high temperatures, such as near exhaust systems or furnaces.
-
Art and Decor: Hose clamps can be creatively used in art and decor, such as creating unique sculptures, light fixtures, or decorative wall mounts. Their industrial aesthetic adds a modern touch to various artistic projects.
-
Automotive Repairs: Hose clamps can be used to secure fuel lines and coolant hoses in automotive applications or even as part of custom engine modifications. Their durability and resistance to harsh conditions suit various automotive needs.
-
Safety Equipment: Hose clamps can secure safety equipment, such as reflective tape or safety lights, ensuring they stay in place and are easily visible.
By exploring these innovative uses, you can find new ways to incorporate hose clamps into various applications, enhancing functionality and creativity.
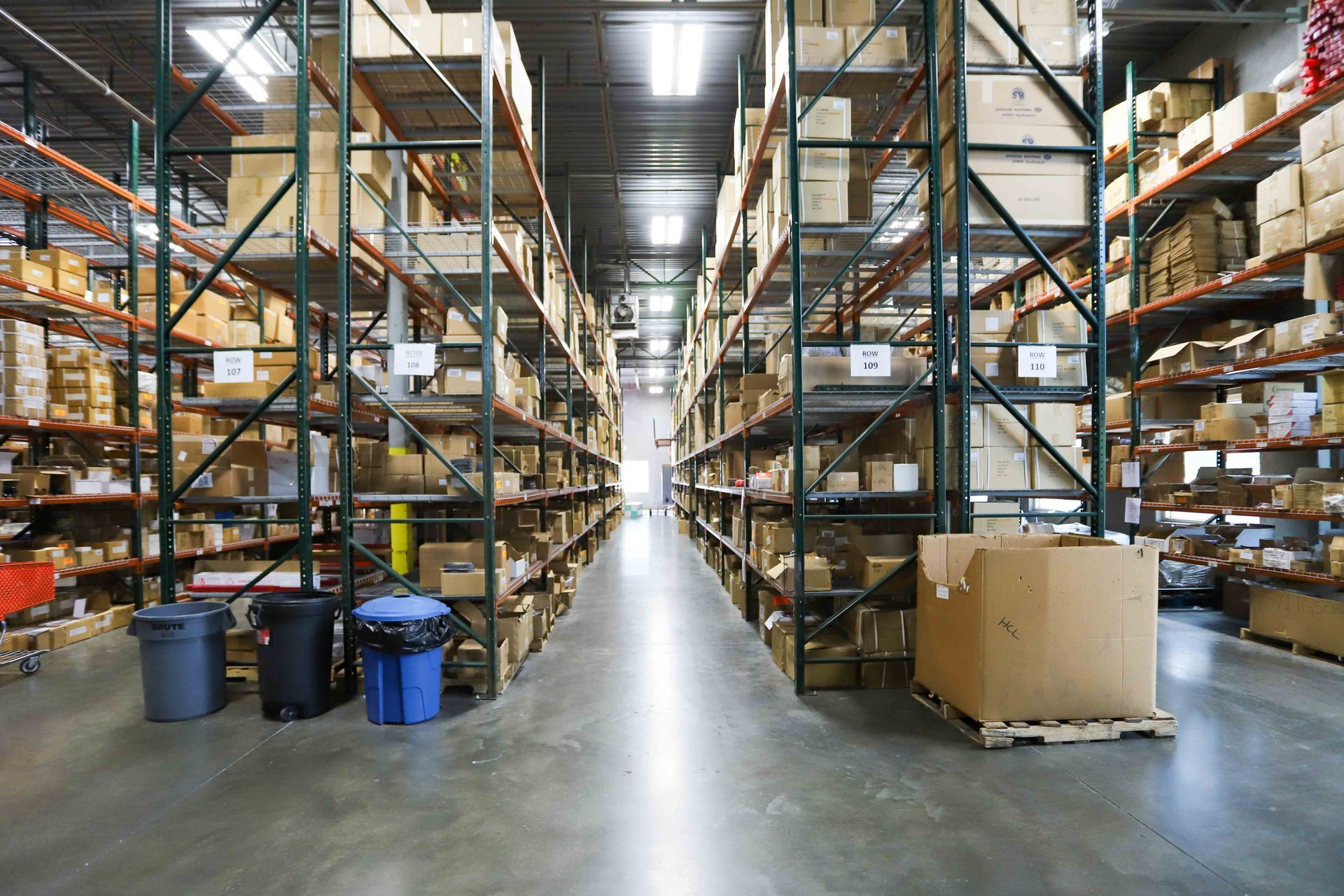
Work With KDAR Company
Selecting the right hose clamps ensures your welding or other industrial projects' safety, reliability, and durability. By considering factors like material compatibility, temperature resistance, pressure ratings, and adjustability, you can prevent premature failures and maintain secure connections.
Whether you are a beginner or an experienced welder, returning to the basics ensures a solid foundation for continued learning and improvement in this vital trade.
At KDAR Company, we strive to provide welders with the equipment (including a large variety of hose clamps)and support they need to do their jobs safely and efficiently, regardless of industry. Contact our support team to learn more!