Why You Should Support American Manufacturing
New and growing companies looking for manufacturers to help produce a project have no shortage of options overseas. However, it’s crucial to consider choosing American manufacturing – especially with the challenges presented with the current state of the supply chain.
We work closely with American manufacturers every day and have learned about the benefits of choosing these relationships and nurturing them. Because we are a smaller family-owned company, you can count on that personalized touch missing from so many companies these days. We like to think we take an old-school approach to meet our clients’ needs, but we also leverage the latest technology to streamline our services.
We are continually adding new and improved products to our lineup. If you see something you like or think of something you need that we don’t offer,
don’t hesitate to reach out! At KDAR Company, our team is always looking for those products that need development, improvement, or a lower cost to acquire. We welcome your ideas and requests for your business.
Here’s just a shortlist of the many benefits of working with US manufacturers and wholesale distributors when it comes time to expand your business footprint.
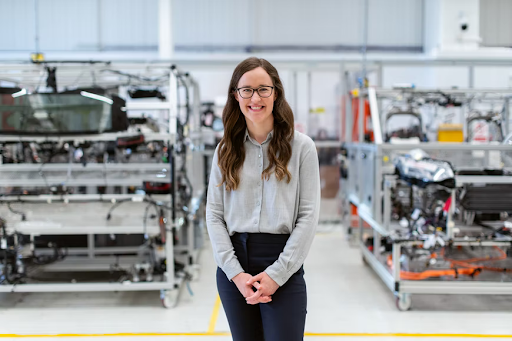
Jobs
By doing business with manufacturers in the US, businesses contribute to economic and job growth in our communities. The country’s Bureau of Labor Statistics reports some of the highest wages for industrial workers within the manufacturing niche and the creation of tens of millions of jobs annually.
Delivery Costs
Overseas manufacturers may offer reduced production costs, but that saving is negated by the cost of shipping and the logistical complications that come with exporting from other countries. US manufacturers can offer lower shipping costs, more means of shipping (i.e. truck, rail, or even barge), and the reduced chance that language barriers will present even more challenges.
Lead Times
The longer it takes for manufactured components to reach a business, the longer the business goes without making money from the finished product. Working with American manufacturers shortens lead times, improves demand forecasting accuracy, and offers a stellar customer experience for shoppers who are used to getting what they want delivered overnight.
Sustainability
Adopting environmentally friendly practices isn’t just good for the climate; it’s great for your bottom line. By choosing to support American manufacturers, you’re investing in an inherently more sustainable relationship because the manufactured goods have much shorter travel and create a much smaller carbon footprint.
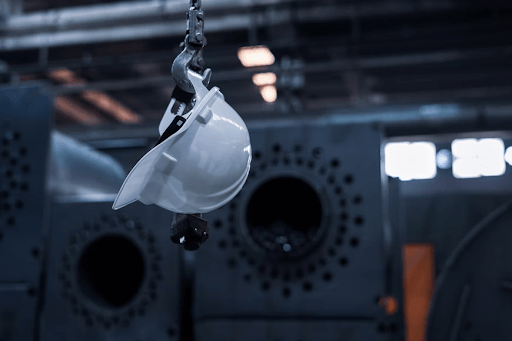
Quality Control
When businesses are close to the manufacturers they work with – like in the same country – it’s much easier to catch a quality control issue before it’s too late and becomes a much costlier mistake. There’s also no confusion regarding necessary safety regulations because American manufacturers are well-versed in the country’s laws and guidelines.
Scalability
New businesses starting with limited budgets and customer bases need to know that their manufacturing partners are ready to grow with them. When within American manufacturers, leaders know that their process and products will be in good hands when it comes time to scale up – all with a quicker turnaround than going overseas.
Worker’s Rights
Unlike many other countries known for their manufacturing capabilities, America has extensive laws in place to protect employees and their rights. Working with US manufacturers means organizations have peace of mind that the workers producing their parts aren’t being exploited or abused to expand profit margins.