How To Safely Store Welding Equipment
Welding is a versatile and essential part of many industries, from construction to automotive manufacturing. Paying close attention to adequately storing welding tools is paramount to ensure workers' safety and equipment longevity. Whether you're a seasoned welder or just starting, these tips will help you maintain a safe workspace while ensuring your welding equipment remains in excellent condition.
Clean and Inspect Equipment Before Storage
Before you even think about storage, cleaning and inspecting your welding equipment is crucial. Over time, tools can accumulate debris, spatter, and contaminants, affecting the quality of your work and posing safety risks. Inspect your equipment for any damage or wear and make necessary repairs or replacements before storing it. This initial step sets the stage for a safer and more efficient work environment when you return to welding.
Avoid Storage Near Flammable Materials
Safety should always be a top priority in a welding environment, and one way to maintain it is by keeping welding equipment away from flammable materials. Welding generates intense heat and sparks, making it crucial to store your gear away from materials like paper, wood, or solvents that could easily catch fire. Using fire-resistant containers or cabinets is an effective way to mitigate potential fire hazards and ensure the safety of your workspace.
Ensure Proper Ventilation
We cannot overstate the importance of proper ventilation in a welding environment. Adequate airing helps disperse harmful welding fumes and gases that can harm your health. Store your welding equipment in an area with good ventilation to maintain a safe workspace. If available, use local exhaust ventilation systems to reduce further exposure to fumes, protecting yourself and any coworkers from the potential health risks associated with welding.
Have A Secure Storage Location
It's essential to store your welding equipment in a secure, designated area. Unauthorized access to these tools can lead to accidents or misuse, so locking cabinets or employing safety cages is an excellent way to ensure that only trained personnel can access the equipment - this protects your equipment and maintains safety in the workplace.
Electrode Storage
Welding electrodes are crucial components in welding, and how you store them directly impacts their performance. Electrodes are susceptible to moisture, so it's essential to keep them in a dry, airtight container to prevent moisture absorption, which can negatively affect the quality of your welding. Store electrodes according to the manufacturer's recommendations, which often include heated cabinets or ovens for moisture control.
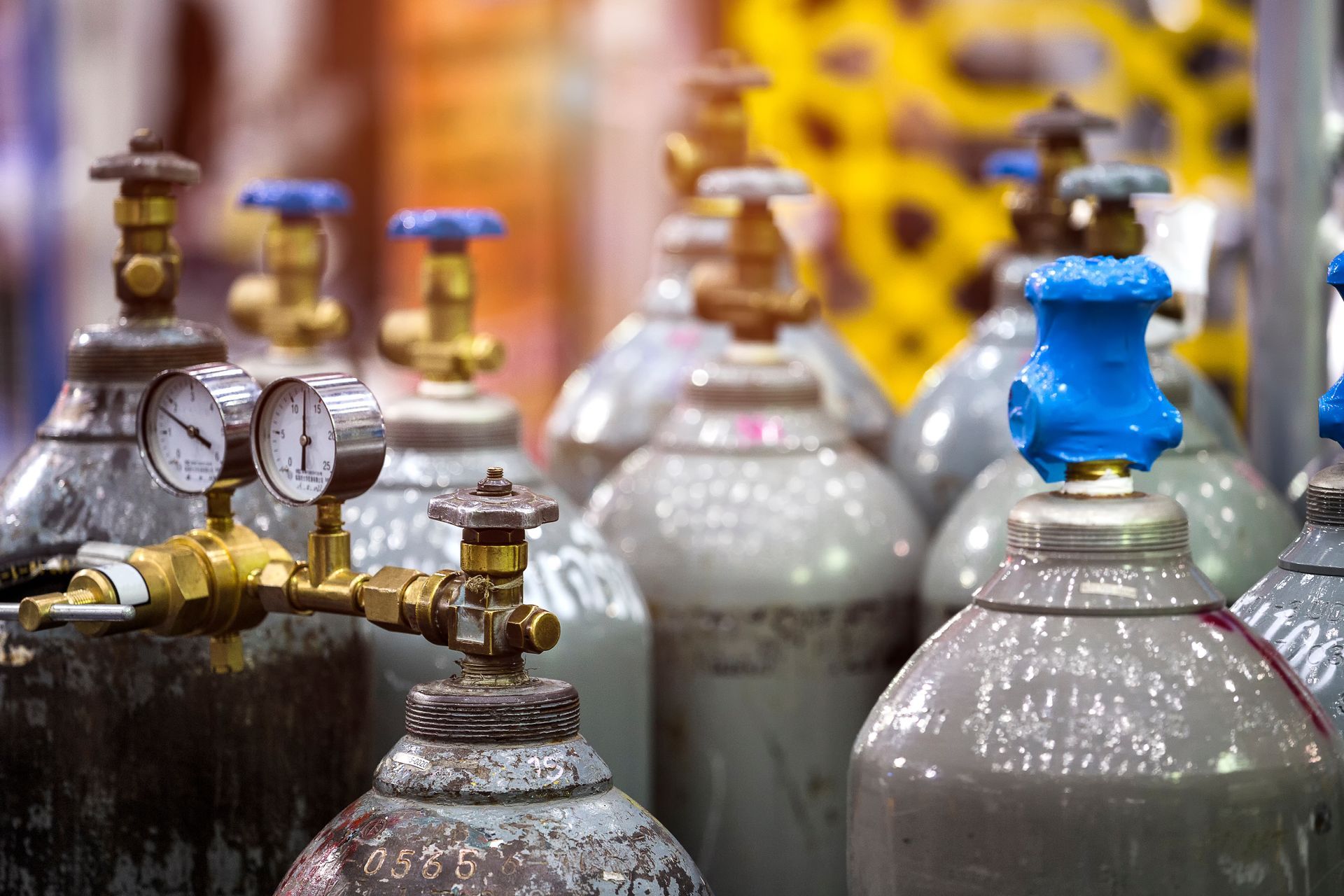
Gas Cylinder Storage
Gas cylinders are another essential welding component, and their proper storage is necessary. Always store gas cylinders in an upright position to prevent tipping. Secure them with chains or straps to ensure they remain in place. Proper labeling is also crucial for identifying the contents of each cylinder, reducing the risk of using the wrong gas, and maintaining safety.
Electrical Safety
Safety extends beyond the storage of welding equipment itself. For electrical welding equipment, it's essential to ensure that it is stored in a dry location to prevent electrical accidents. Disconnect the power source and turn it off when the equipment is unused. Following these electrical safety practices during storage can significantly reduce the risk of accidents caused by electrical malfunctions or mishandling.
Employ An Organized Storage System
An organized workspace is not only more efficient, it is safer. Labeling shelves, bins, or racks for your welding equipment keeps everything in its place and easily accessible; this reduces the risk of accidents caused by clutter and saves time when you need to locate specific tools quickly. Invest in proper storage solutions and commit to an organized system to ensure a safer and more efficient workspace.
Use Protective Covers
Protective covers are an often overlooked aspect of proper storage for welding equipment. By covering your welding machines and equipment with protective covers or tarps, you shield them from dust, debris, and potential damage during storage. These covers act as a barrier, preserving the integrity of your equipment and extending its lifespan.
Perform Regular Maintenance
Maintenance should be a continuous practice, even during storage. Establish a routine maintenance schedule to inspect and service your welding equipment to ensure that your tools remain in optimal condition when needed, reducing downtime, costly repairs, and safety risks. Regular maintenance also serves as a preventive measure against accidents caused by malfunctioning equipment.
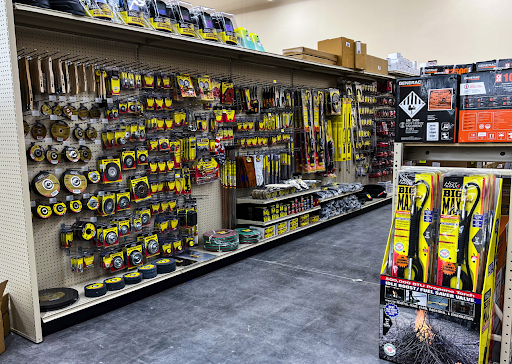
Work With KDAR Company
Properly storing welding equipment isn't just a matter of convenience; it's critical to maintaining a safe and efficient workspace. By following these ten tips, you can ensure that your equipment remains in excellent condition and that your workplace is free from unnecessary safety hazards. Remember, safety should always come first when working with welding equipment. Implement these tips, and you'll reduce the risk of accidents and extend the life of your valuable tools, ultimately saving time and money in the long run. So, make safety a priority, and your welding workspace will thrive.
For all your wholesale needs, including cable ties, welding equipment, and pressure washer accessories, KDAR Company is here to support you. We offer a comprehensive range of wholesale merchandise to cater to your specific requirements. Contact us today for further inquiries or to place an order. Let KDAR Company be your trusted partner in the world of welding.