Which Hose Clamp Works Best For My Project?
Are you starting a project and needing hose clamps? Hose clamps are vital for ensuring secure connections between hoses and fittings. However, choosing the correct hose clamps for your project is crucial for achieving optimal performance, safety, and durability.
Our latest blog post explores tips to help you select the perfect hose clamps for all your project needs.
Material Compatibility
Material compatibility is the first consideration when selecting hose clamps. Stainless steel hose clamps are commonly preferred due to their excellent corrosion resistance and ability to withstand high temperatures. Ensure the hose clamp material aligns with the environment to prevent premature failure and ensure longevity.
Temperature Resistance
Choosing stainless steel hose clamps that are capable of withstanding a broad temperature range of your application is essential.
Pressure Ratings
Different systems often operate under varying pressure levels. Selecting hose clamps with appropriate pressure ratings is vital to prevent leaks or blowouts. Consider the maximum pressure your setup may encounter and choose hose clamps that can handle those pressures safely and reliably.
Corrosion Resistance
Outdoor or salt water environments can be especially harsh, with exposure to moisture, chemicals, and other corrosive agents. Opt for hose clamps with excellent corrosion resistance to ensure longevity and reliability in challenging conditions. Stainless steel hose clamps are popular for their corrosion resistance, making them ideal for almost all but the harshest environments.
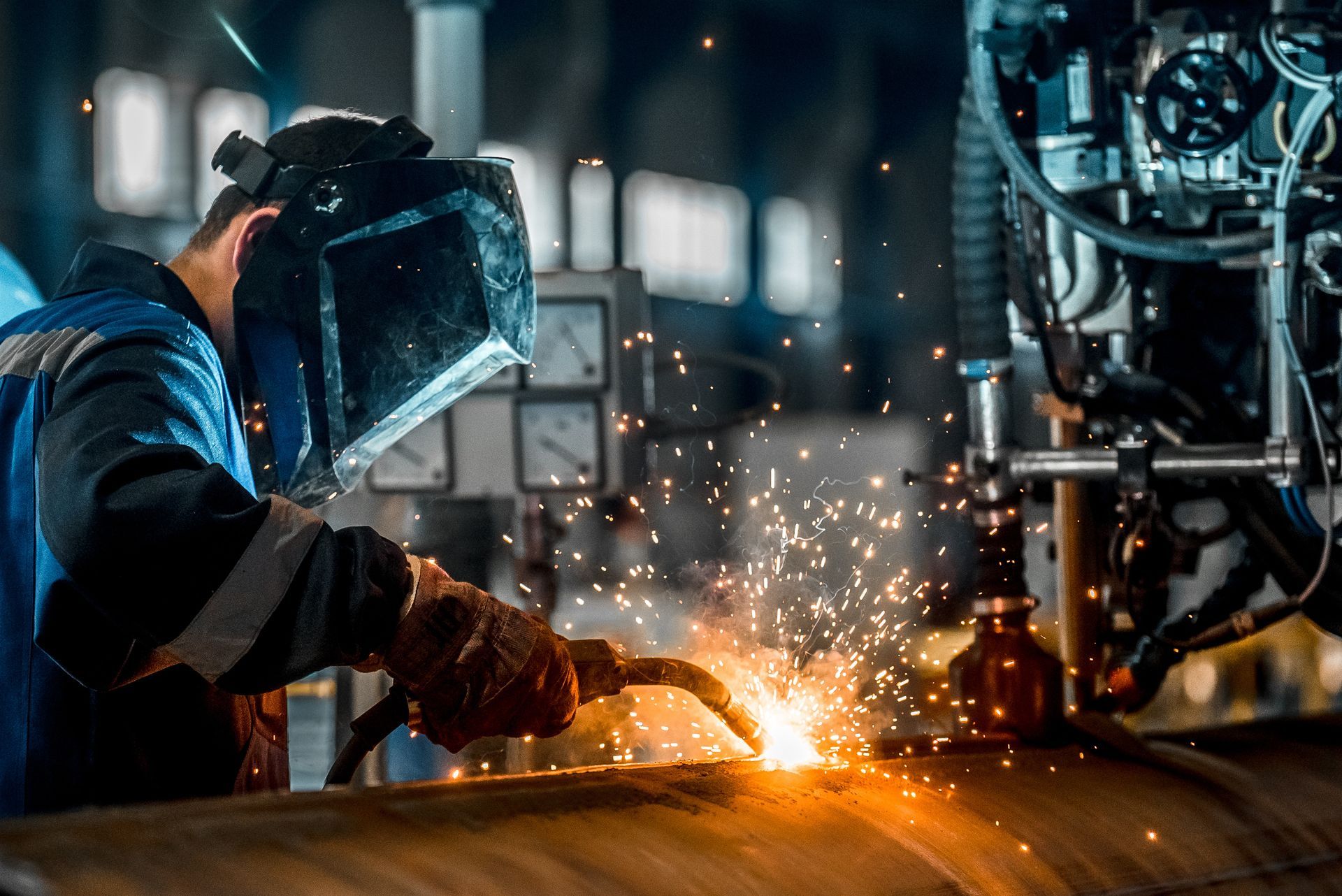
Size and Diameter
Proper sizing of hose clamps is critical to achieving a secure and leak-free connection. Ensure the hose clamps you choose match the size and diameter of your hoses accurately. Using incorrectly sized clamps can lead to leaks, hose damage, and compromised performance in your application.
Installation Method
Different hose clamps require different installation methods. Some may require tools like screwdrivers or wrenches, while others feature quick-release mechanisms for easy installation. Consider the installation process and choose hose clamps that align with your workflow and efficiency requirements to streamline your project.
Adjustability
Different projects may require hose tightness or diameter adjustments over time. Select hose clamps that offer adjustability to accommodate changes in hose size or tension requirements. Worm drive hose clamps, for example, provide adjustable tightening for a secure and customizable fit.
Vibration Resistance
Vibrations can loosen hose connections over time, leading to leaks or equipment damage. Choose hose clamps with features like locking mechanisms or constant tension designs to withstand vibrations and maintain a secure seal.
Accessibility
Consider the accessibility of hose clamps, especially in tight or hard-to-reach spaces within your setup. Opt for hose clamps that are easy to access for installation, adjustment, and maintenance to minimize downtime and enhance efficiency in your operation.
Specialized Applications
Some projects may require specialized hose clamps for specific purposes, such as high-pressure applications, extreme temperatures, or chemical resistance. Familiarize yourself with the available options and select hose clamps tailored to your unique requirements for optimal performance and safety.
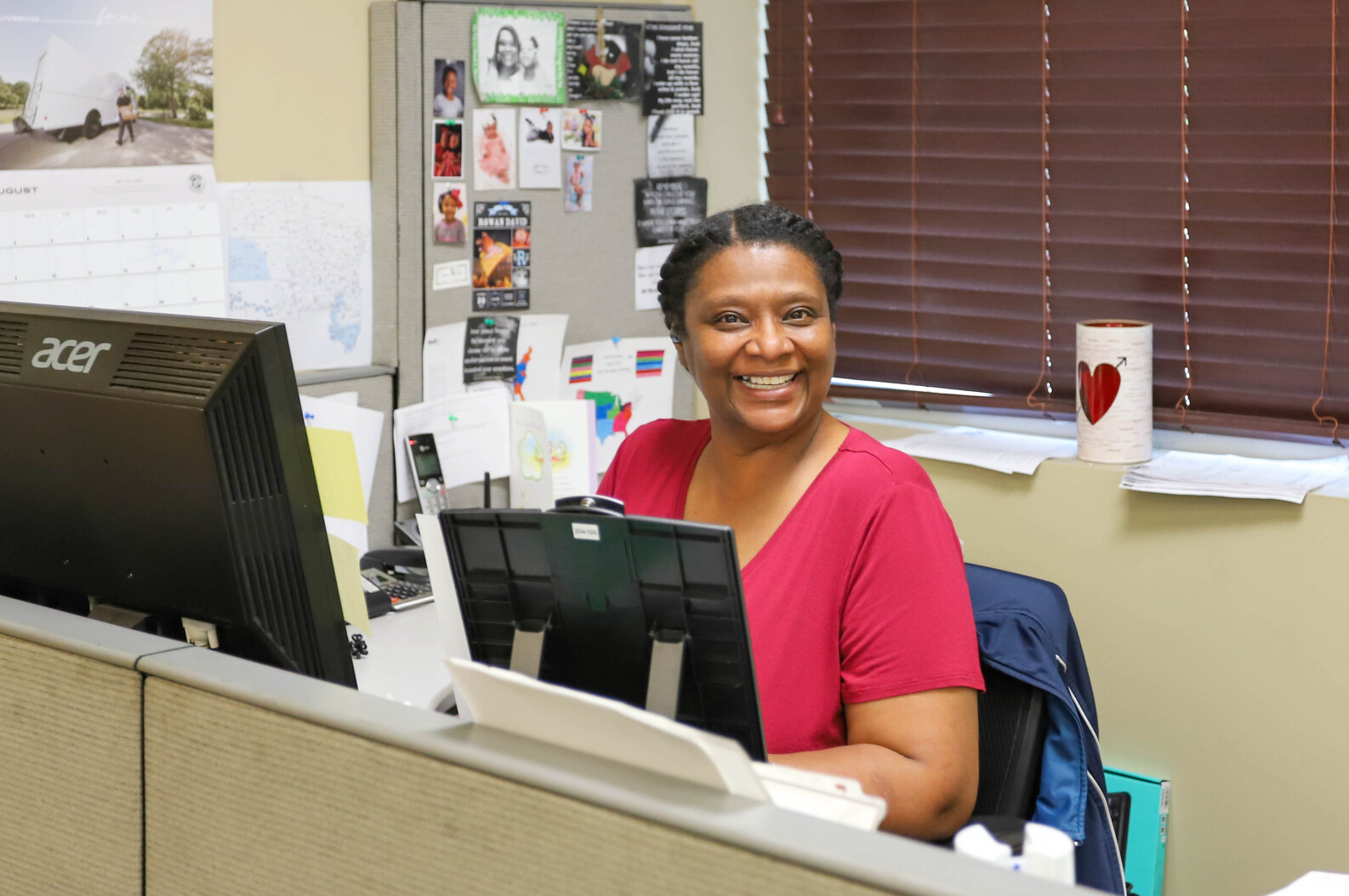
Work With KDAR Company
Choosing the correct hose clamps is essential for the success of your welding projects. By following these ten important tips, you can ensure reliable performance, safety, and efficiency in your welding operations.
For all your wholesale needs, including cable ties, welding equipment, and pressure washer accessories, KDAR Company is here to support you. We offer a comprehensive range of wholesale merchandise to cater to your specific requirements. Contact us today for further inquiries or to place an order. Let KDAR Company be your trusted partner in welding and beyond.