5 Unique Types of Welding
Modern welding has been around for decades, and new techniques, equipment, and skill sets come with each generation. Many industries have welders involved in some capacity. Because of this, one crucial aspect of welding is understanding the different welding techniques available. In this blog post, we will delve into five unique types of welding: Plasma arc welding (PAW), resistance welding, thermit welding, submerged arc welding (SAW), and flux-cored arc welding (FCAW). By exploring these specialized techniques, you can gain insights into their applications and make informed decisions for your welding projects.
Plasma Arc Welding (PAW)
Plasma arc welding is a precise and efficient technique that utilizes a highly concentrated plasma arc to weld materials. This process involves creating an ionized gas plasma that reaches temperatures up to 30,000°F. PAW is commonly used for applications that require exceptional weld quality, such as aerospace, automotive, and nuclear industries. Its advantages include high accuracy, minimal distortion, and excellent control over the heat-affected zone. PAW equipment typically includes a power supply, torch, gas control system, and filler material.
Resistance Welding
Resistance Welding is a joining process that relies on the resistance heating of the workpieces. The resistance to the flow of electric current through the welded materials generates heat. This technique is widely used for spot, projection, and seam welding applications. Resistance welding offers several advantages, including high production rates, minimal heat-affected zone, and suitability for automation. The equipment required for resistance welding includes a power supply, electrodes, and a control system.
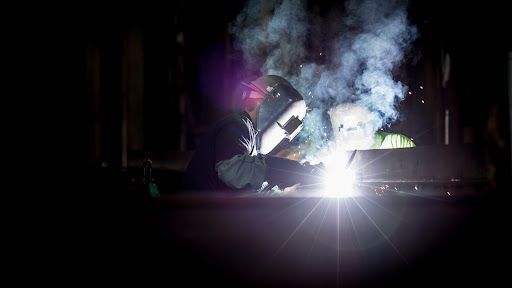
Thermit Welding
Thermit welding, or exothermic welding, is a fusion welding process that utilizes a chemical reaction between aluminum powder and metal oxide. This reaction generates intense heat, reaching temperatures of around 3,500°F, which is used to melt and fuse the workpieces. Thermit welding is commonly used for joining railroad tracks, heavy machinery parts, and pipelines. Its advantages include excellent joint strength, minimal distortion, and the ability to weld dissimilar metals. The equipment for thermit welding typically consists of a crucible, molds, igniter, and pouring equipment.
Submerged Arc Welding (SAW)
Submerged arc welding is a technique that involves the formation of an arc between a continuously fed wire electrode and the workpiece. The weld area is shielded by a layer of granular flux, which protects the molten metal from atmospheric contamination. SAW is widely used in shipbuilding, construction, and pressure vessel manufacturing industries. Its advantages include high deposition rates, deep penetration, and excellent weld quality. SAW equipment typically consists of a power source, wire feeder, welding head, and flux recovery system.
Flux-Cored Arc Welding (FCAW)
Flux-cored arc welding is a semi-automatic or automatic welding process that uses a tubular wire electrode with a flux-filled core. The flux provides shielding and protective gas, eliminating the need for an external shielding gas. FCAW is commonly employed in heavy fabrication, structural welding, and offshore applications. Its advantages include high deposition rates, excellent weld penetration, and versatility in welding thick materials. FCAW equipment comprises a power source, wire feeder, welding gun, and flux-cored wire.
Understanding the diverse types of welding techniques is crucial for selecting the most suitable method for your specific applications. Each technique offers distinct advantages and finds its place in various industries. By familiarizing yourself with these welding types, you can make informed decisions and achieve optimal results in your welding projects.
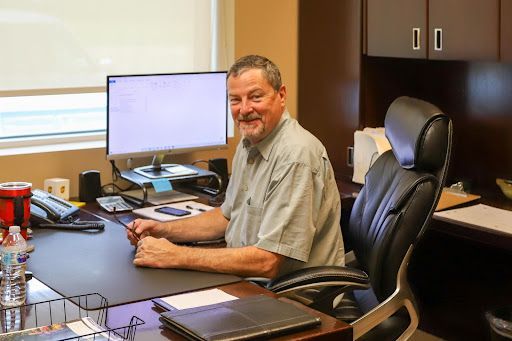
Work With KDAR
For all your wholesale needs, including cable ties, welding equipment, and pressure washer accessories, KDAR Company is here to support you. We offer a comprehensive range of wholesale merchandise to cater to your specific requirements. Contact us today for further inquiries or to place an order. Let KDAR Company be your trusted partner in the world of welding.